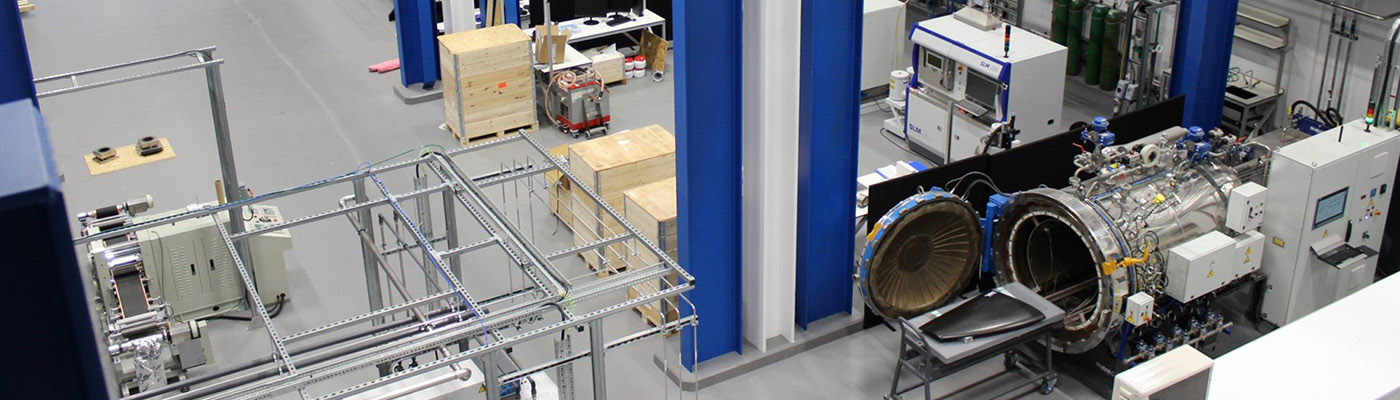
Composite materials
Whether in fibre-reinforced composites, polymers and rubber, graphene has a host of possible enhancements it can offer to each with numerous transformative properties.
The Composites facilities within the GEIC are designed to give our members and partners access to pilot-scale production equipment that will meet all of their requirements and help exploit the potential of graphene-enhanced composites. Also, in receiving access to academics working solely on graphene and 2D materials, our partners benefit from support and knowledge at The University of Manchester that is second to none.
Composites formulation
The Composites formulation lab allows access to all the necessary equipment for processing resin systems, polymers and rubbers of many different types.
The lab equipment includes:
- bench space and fume cupboard access
- tools such as paddle mixers, Silverson high shear mixers and SpeedMixers for producing resin systems
- Resodyn LabRAM II Acoustic mixer for mixing powders, liquids and coating pellets
- 2 and 3 roll mills for processing resins and rubbers
- Rheometer for the characterisation of rheological properties
Please contact us for more information on pricing and availability.
Processing lab and High Bay
Our processing lab and High Bay areas house the pilot scale equipment needed for producing polymers, rubbers, fibre reinforced products, mixed metal composites and ceramics to our customers specifications.
The processing lab equipment includes:
- Internal mixer with multiple screw types, process monitoring and a max temperature of 450°C
- HAAKE twin screw extruder with multiple screw types and configurations, including a single screw option. Various outputs comprising pellets, filaments and blown films. Maximum temperature is 450°C covering a full range of thermoplastics
- FANUC Roboshot S 50i A Injection Moulder, capable of up to 450°C max temp and 50 Tons clamping pressure
- PEI LAB250P hot press, has a platen size of 400mm x 400mm, daylight of 450mm, maximum pressure of 60 Tons and a max temperature of 450°C
- Labortech Mechanical Tester, which has a 5kN load cell used for testing polymers and a 200kN load cell for FRP’s, both work with either the extensometer or deflectometer for modulus calculations. The testing speeds range from 0.0005 to 1000mm/s.
The High Bay equipment includes:
- Our Autoclave has working dimensions of Ø1m x 1.5m and is capable of a maximum temperature of 410°C and 7bar (100psi) pressure enabling us to process thermoset and thermoplastic materials
- Spark plasma sintering furnace FCT HP D – SD, enables us to sinter composite materials, aluminium, copper alloys and structural and functional ceramics. The max component size is Ø50mm, pressing force of 100kN, voltage 7.2V, current 8000A and a working temperature up to 2200°C
- High temperature vacuum sintering furnace – FH W 9 SD which processes MMCs and CMCs. It has graphite cleaning capability both inert and vacuum atmosphere and has a max temperature of 2200°C
- Tube furnaces: Carbolite Gero – HTRH-3 and FZS 3. Both the HTRH-3 and FZ 3 are used for general thermal processing such as annealing, carbonisation, sintering and drying. The difference between the two is that the HTRH-3 has a mx temperature of 1600°C and the FZ 3 has a max temperature of 1300°C.
Please contact us for more information on pricing and availability.
Our team
- John Vickers - Application Specialist
- Mark Dickie - Application Manager, Composite Materials
- Scott Boardman - Application Specialist
My team and I are here to support your business and have many years of experience to guide experimental design and rapid product development en route to market. We have worked across numerous sectors that can benefit from the use of graphene and 2D materials in composites and we’re at your disposal to discuss innovative concepts and projects.
Mark Dickie / Application Manager